Optimise Plant Performance in Chemical Facilities Using Continuous Circuit Diagram This research outlines the mechanisms of corrosion, the challenges of current monitoring methods, and presents a framework for the deployment of IoT in corrosion management. View full-text Article The Benefits of Implementing IoT for Corrosion Monitoring. As previously mentioned, IoT permits continuous, real-time, and accurate monitoring of oil and gas assets (pipelines, process vessels, tank farms, etc.) for corrosion-related defects. This allows faults to be detected in the early stages, thus minimizing repair work and associated downtime.
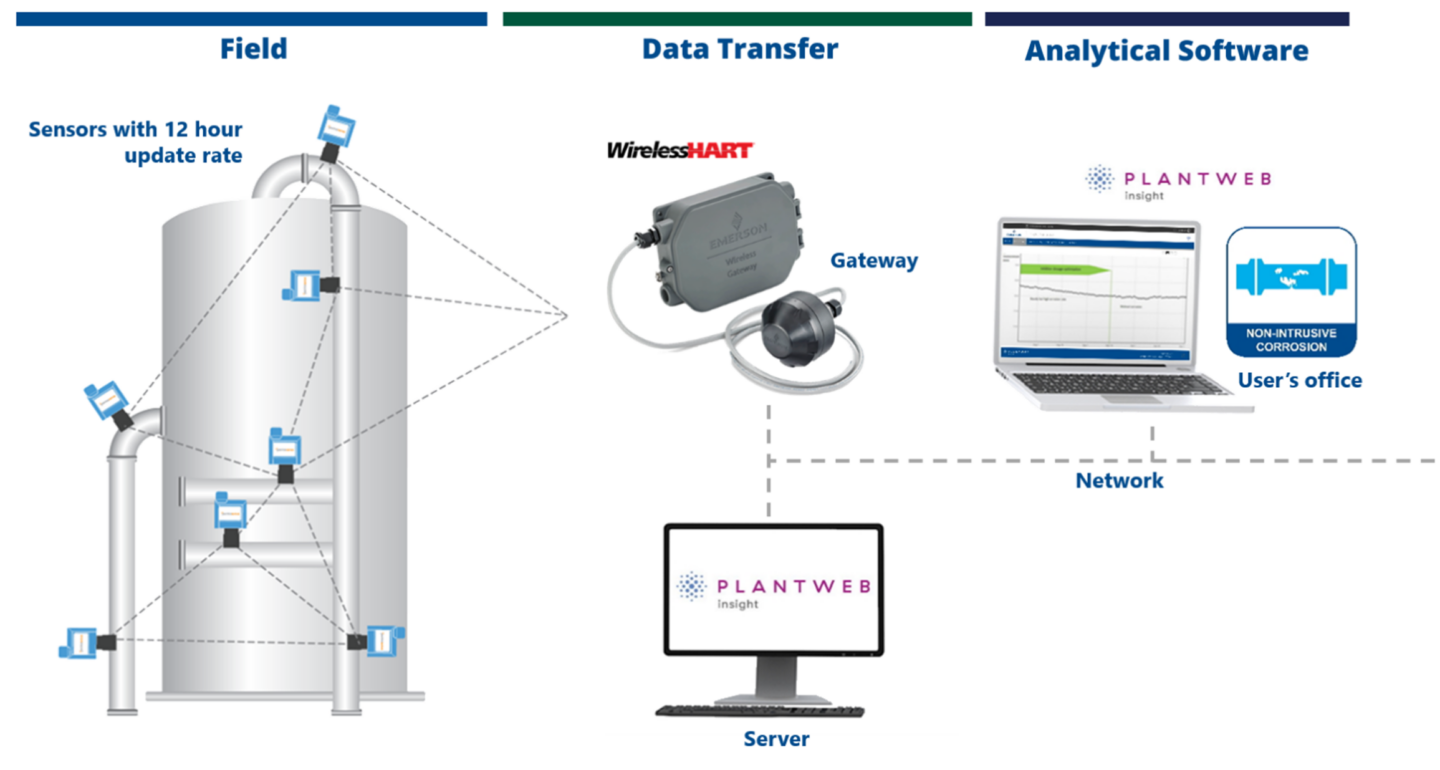
As you have learned in this post, you can build an IoT-based automated pipeline inspection system to store your data in a data lake. The data coming from various ultrasonic sensors is then stored in S3 where you can perform analytics on the data using Athena. Visual dashboards are generated using QuickSight.
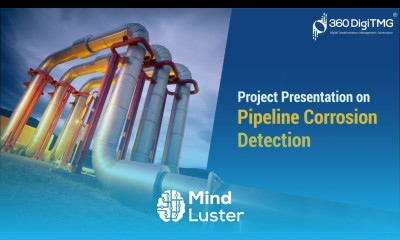
IoT for Corrosion Monitoring in the Oil and Gas Industry Circuit Diagram
For instance, implementing real-time monitoring can reduce maintenance costs by up to 30% and prevent losses associated with pipeline failures, which can amount to millions of dollars per incident. The adoption of real-time corrosion monitoring solutions represents a significant advancement in maintaining pipeline integrity. Case Study: Real-Time Pipeline Monitoring and Leak Detection with IoT Background XYZ Pipeline Company (Note: For the purpose of this report, we will refer to the company as XYZ Pipeline Company), a major player in the oil and gas sector, operates an extensive network of pipelines spanning thousands of kilometers across diverse terrains.
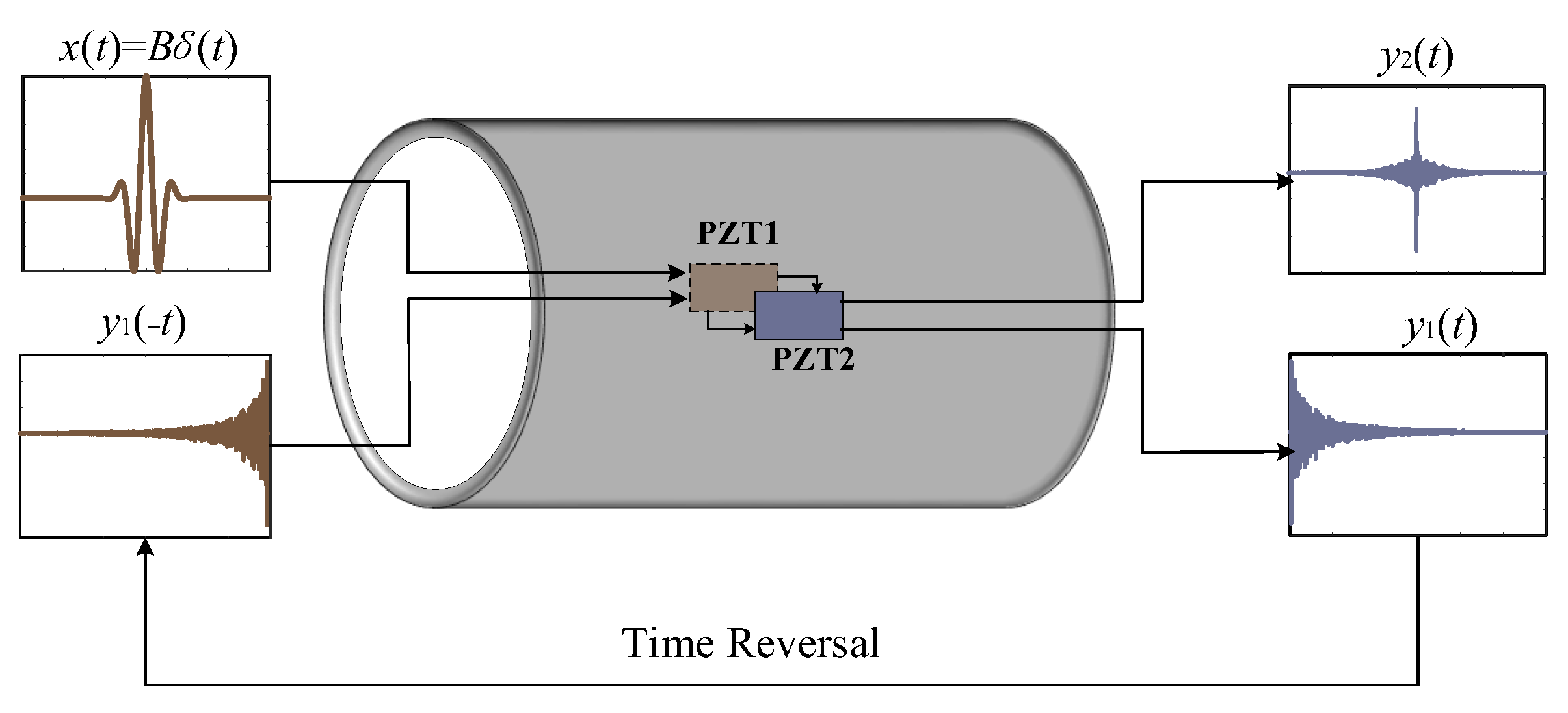
The Internet of Things (IoT) provides an opportunity for realizing the real-time monitoring system by deploying the IoT-enabled end devices on the oil pipeline. In this study, we propose a hybrid architecture based on 2.4 GHz-based Zigbee and LoRa communication for oil pipeline monitoring. - Referred to as a "real time on-line" monitoring - Corrosion rates are measured directly - Inspection pigs gather information about the pipeline, which can include temperature and pressure, corrosion / metal loss, diameter, bends and curvature. โข Fixed in place requires system depressurization โข Safely inserted and retracted at all of an ultrasonic monitoring device for pipeline corrosion in a specific oil and gasfield has been investigated in this paper. Researching the gathered real time data and mining the data gives more insights into tackling the corrosion monitoring. There is also scope for analyzing and understanding why and how corrosion happens, how the environment

Time Oil and Gas Pipeline Monitoring with IoT Circuit Diagram
Companies that apply IoT-based systems in corrosion monitoring. Next, I will mention some outstanding companies in this field: Aegion Corporation: Aegion is a leading provider of infrastructure protection and rehabilitation services, including IoT-based corrosion monitoring systems. They offer integral solutions for the detection and prevention of corrosion in sectors such as oil and gas
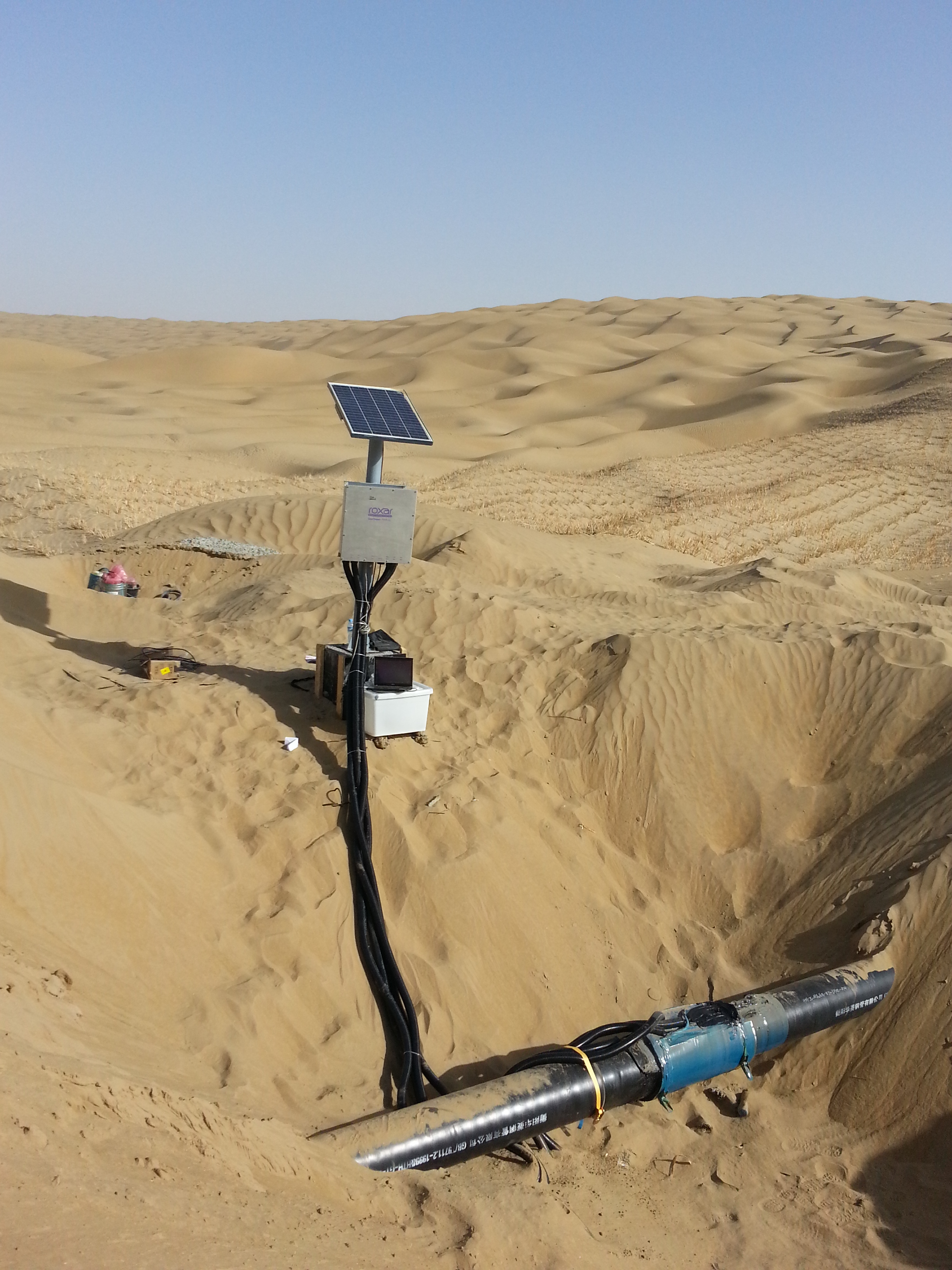